| Published June 22nd, 2011 | Orinda's Windsor Chair Guy-George Lucido | By Andrea A. Firth | 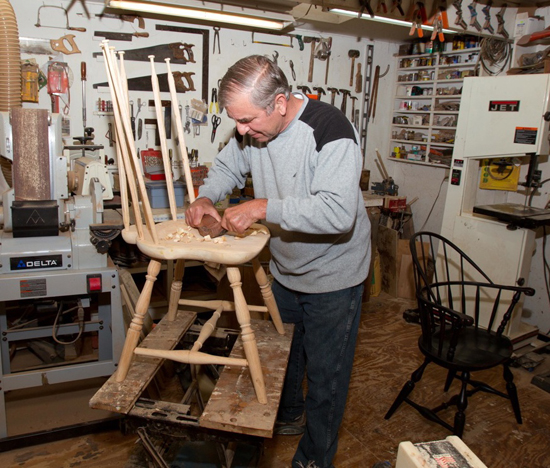 | George Lucido at work on a chair in his workshop . Photos Doug Kohen
| George Lucido was destined to work with wood. One of the first things he did when he moved to Orinda in 1984 was build a workshop out back, a small space of his own where he taught himself to carve wood. The walls of the workshop are lined with a collection of tools passed down by his grandfather, Orlando Pasquinucci, a shipbuilder in San Francisco around the turn of the century, and his father, Neno Lucido, who spent his career as a finish carpenter. "It's in my genes, I guess," says Lucido.
After retiring as an aerospace engineer eleven years ago, Lucido has focused his extensive energy on woodworking. The workshop has been bumped out a few feet on two sides to accommodate his growing collection of tools, equipment, and wood. And about three years ago, he started to take classes at the Mount Diablo Adult Education Center where he met another Orinda resident, Tom Killen, a master woodworker who specializes in colonial furniture. It was Killen who introduced Lucido to the art of the Windsor chair.
An easy going and patient man with an engineer's focus on design and detail, Lucido had the right temperament and skill set to quickly master the complex and time consuming construction of the American Windsor chair-the elegant and lightweight wood chair of royal English roots with a gently curved back formed by turned spindles connected to a thick carved seat, supported by splayed legs plugged into the underside. Once called stick chairs, Lucido has made five of the seven varieties of the American Windsor chair, and a total of seven Windsors in all.
Lucido brings a mix of art, science, and tenacity to his Windsor chair building. He estimates that each chair requires 120 to 150 hours to build over a three-month period. Lucido researches every aspect of the chairs he reproduces, and each project typically starts with him creating a comprehensive, hand-drawn plan.
"I like to keep it as authentic as possible. All of the chairs were built the original way using the original tools," says Lucido. When unable to find a domestic source for an English travisher, a convex woodcarving tool used for shaping the chair's seat, Lucido made one himself. He smiles when pointing out the exception - he admits freely to using an electric-powered lathe versus the pedal-powered lathe employed in the early days.
The wood and paint he uses are also original. The chair seats are made with Eastern white pine sourced from the East coast, and the rest of the chair is made with freshly cut Modesto Ash, a tree common to the Bay Area with wood that has a very straight grain, so it bends easily and works well for the curved pieces on the chair back. Lucido covers the chairs with two coats of milk paint (an all natural product), first red then black. "When the chairs were first made, they were mostly painted red because that pigment was more readily available and then in later years re-covered with black paint," explains Lucido. He burnishes the black layer to create a shiny and silky smooth surface and leaves streaks of the rustic red peeking through at the edges.
Lucido's woodworking craft is in large part self-taught, and he has kept busy sharing his knowledge. He volunteers time in the advanced woodworking class at Campolindo High School, and he occasionally gives talks to community groups about his craft.
"It's a really fun hobby. I'm out here in the workshop seven days a week," he says, "It doesn't give me the frustrations that a relaxing day on the golf course used to." And as a reminder, should he be tempted to forgo the woodshop and return to the links, Lucido has his driver prominently displayed over the doorway of his workshop-and that's where it will stay, says Lucido..
George Lucido also does wood furniture repair. You can reach him at his studio at (925) 254-3659 or via email at sawdustman1@comcast.net.


|
More About the American Windsor Chair
Like many of the things that migrated with the early colonists, Windsor chairs were remade with an American twist. In England, chair makers were required to belong to a guild, which dictated the chair design and amount to be charged. The colonists quickly discarded the old world constraints and created their own chair designs, and the seven varieties of the American Windsor chair were born.
So why were they called "Windsor" chairs? As one story goes, King George was hunting and took refuge from the rain in a farmer's house in the woods. While there he sat in the farmer's chair and found it so comfortable that he ordered several identical chairs to be produced for his home, Windsor Castle. (George Lucido finds this explanation a bit far-fetched.) More likely, the name stems from the fact that the chairs were first made in Windsor, England, an area where many of the woods used could be sourced.
The quintessentially American Windsor chair has been seen throughout the United States' brief history and carries a democratic provenance.
- George Washington was a devoted Windsor chair collector and had 27 Windsors at his Mount Vernon home.
- Thomas Jefferson wrote a draft of the Declaration of Independence while seated in a Windsor.
- When the Declaration of Independence was signed in Philadelphia on July 4, 1776, the assembly sat in Windsors.
- Washington's officers sat in Windsor chairs at Fraunces Tavern in New York City to listen to his farewell speech.
[Source: http://www.gummelchairworks.com/Windsor-Chair-History.htm]
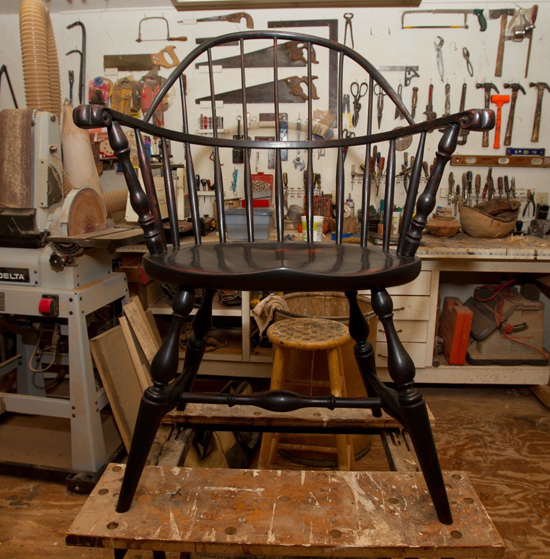 | A sack back American Windsor chair.
|
George's Bowls and Vessels
People call George Lucido when a tree falls. "It happens all the time," he says. And when he gets a call, he gets to work right away (the wood must be harvested within a week) turning the dead tree remnants into beautiful and functional bowls. Lucido has collected wood from felled trees such as black acacia, black walnut, and birch, from all over Contra Costa County. After making the bowl, he allows it to cure for a year and then sands, oils, and polishes it to provide a bright, natural sheen.
Lucido also makes some very elaborately detailed bowls and vessels, which are more about art than function. The woodworker uses popular and exotic woods to recreate the designs of clay vessels from the Southwest. These bowls and vessels are sold at Valley Art in Walnut Creek and Gallery M in Half Moon Bay.
A. Firth
|
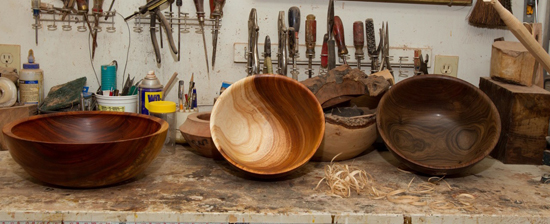 |
| 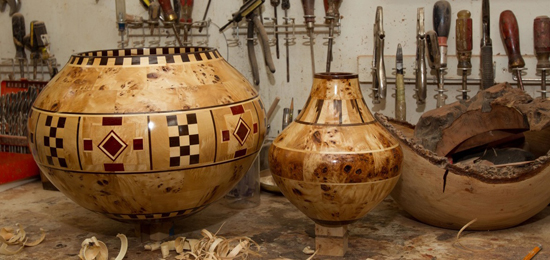 | Photos Doug Kohen
| | | | | | | Advertisement | | | | | | print story Before you print this article, please remember that it will remain in our archive for you to visit anytime. download pdf (use the pdf document for best printing results!) | | | Comments | | | | | | | | | | | | | | | | | | | |